

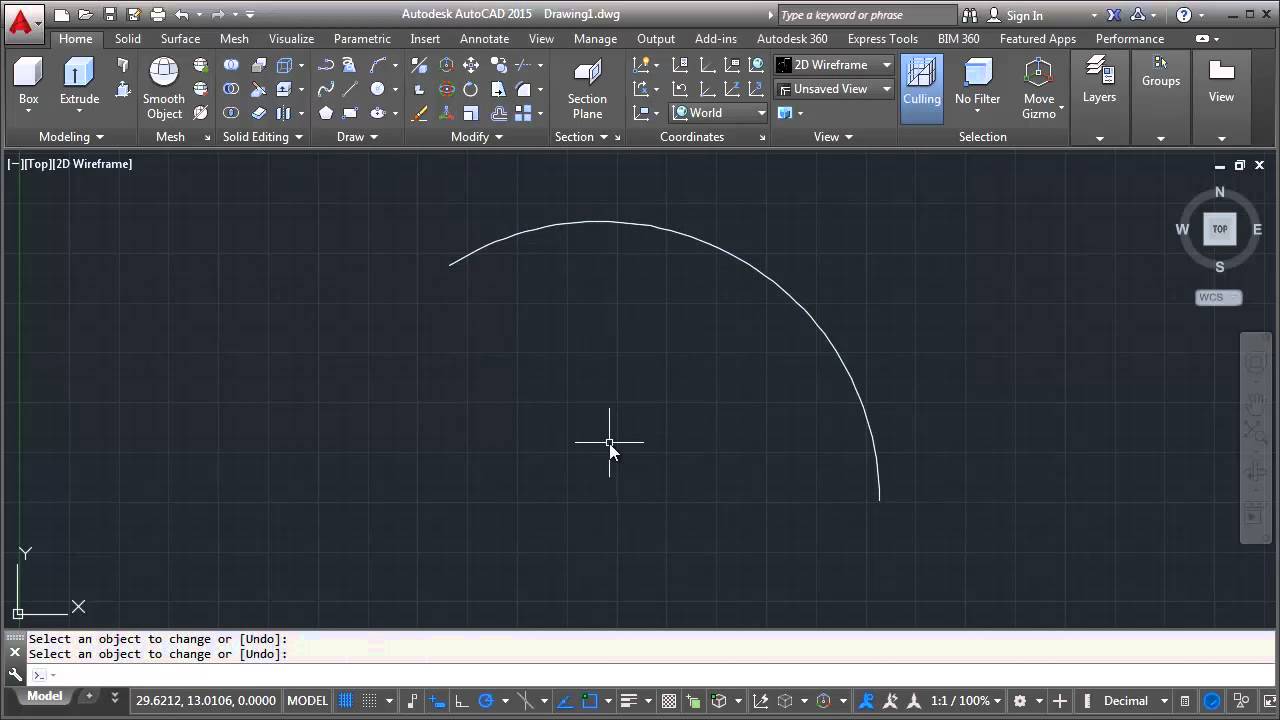
Obtaining the experimental data did possibly using the roughness tester as a measuring device. The cutting regime adapted to carrying out the necessary experiments supposes a constant cutting speed, while the cutting depth varies with different values. The active experiment is the research method used to achieve the proposed objective. The primary objective of this paper is to track the evolution of the surface roughness measured longitudinally on the feed motion direction in the end-milling process of an aluminum alloy used in the aerospace industry. This paper is a continuation of our previous research. The surface quality study of the cutting processes is a very current and complex subject, which approached in variously specialized researches. List of Honorary Committee, Scientific Committee, Organizing Committee, Keynote Speakers, Conference Chair, Sections Chairs, Sponsors and Partners are available in this PDF. Over the last few years, other departments from universities in Romania (Braşov, Bucureşti, Cluj, Galaţi and Piteşti) or other countries (Serbia, Greece) have been involved in organizing the conference. By considering the new trends and requests valid in the field of manufacturing engineering from the entire world, starting from 2013, the name of the conference was changed in "Innovative Manufacturing Engineering" and later in "Innovative Manufacturing Engineering and Energy". The first conference was organized in May 1996 at Iaşi and, since 1999, the conferences have been organized alternately, in Iaşi and Chişinău, by the collaboration of the Machine Manufacturing Departments from the "Gheorghe Asachi" Technical University of Iaşi (Romania) and from the Technical University of Moldova from Chisinau (Republic of Moldova). Estimated time for completion: 5 minutes.The 23 rd edition of Innovative Manufacturing Engineering & Energy International Conference (IManEE 2019) is the result of a collaboration between the Department of Manufacturing and Industrial Management of the University of Piteşti (Romania) and the Department of Manufacturing Engineering of the "Gheorghe Asachi" Technical University of Iaşi (Romania). Try the following statements at the Command line, first using the (setq) command to specify several points, and then executing AutoCAD commands through AutoLISP. ( command “pline” POINT1 “w” STARTING_WIDTH ENDING_WIDTH POINT2 “”)Ĭommand: pline Specify start point: 2,2 Current line-width is 0.0000 Specify next point or : w ( setq STARTING_WIDTH 0.1 ENDING_WIDTH 0.1 POINT1 “2,2” POINT2 “4,4” ) See also inspecting values with autolisp in AutoCADĬommand: circle Specify center point for circle or : Specify radius of circle or : 2 Command: nil The (command) function always returns nil.Ĭommand: line Specify first point: 0,0 Specify next point or : 1,5 Specify next point or : Command: nil The (command) function with no arguments is equivalent to canceling the active command. The null string “” is the equivalent of hitting the spacebar or key in AutoCAD.Use the predefined symbol PAUSE to wait for user input.( setq RADIUS 1.25) ( command “circle” “4,4” RADIUS) You can include any AutoLISP symbol or expression that evaluates to an appropriate value.AutoCAD commands and options are typed in as strings.It is followed by the command’s options input in the same order they would be typed at the AutoCAD “Command:” prompt. The first argument to the (command) function is always the command name. Rather than have an entirely new set of drawing and editing commands, AutoLISP permits the user to tap all of AutoCAD’s existing commands from within AutoLISP using the (command) function.
